Ordinary cold forging
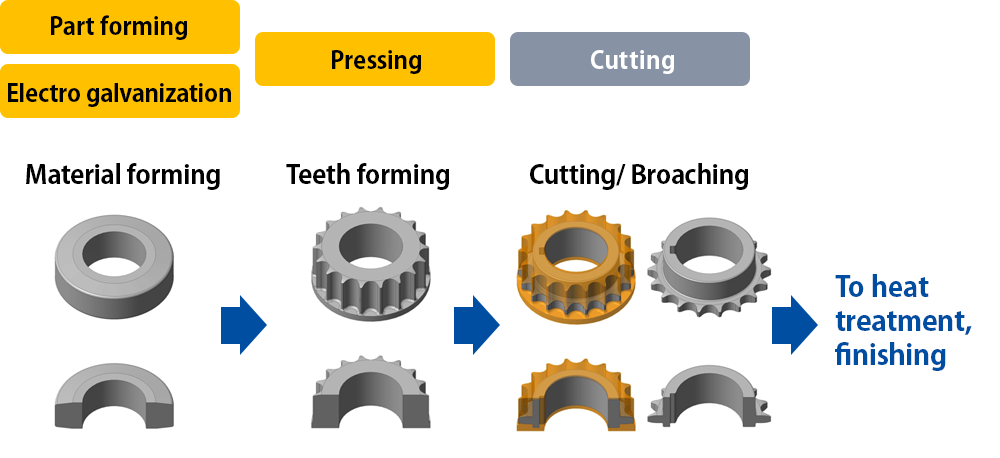
Technology - Core technology
Our original “SOSEI-FORMA technology” was developed based on skills that have been refined through the production of chains and other components. Various phenomena occurring in press forming are analyzed according to the plasticity theory, and the press load is optimized by adjusting processing conditions, dies and special devices. Thus, the press forming of products in complex shapes is possible while maintaining a processed surface condition equivalent to fine blanking. This technology has produced much value via net shape processing, such as cost reduction and contribution to the promotion of a low-carbon society.
*Net shape processing: Finish processing (cutting, etc.) is not required to complete products.
Complex, fine 3D shapes can be formed via net shape processing
×
Shear droop and fracturing are prevented to the utmost
Surface roughness and dimensional accuracy are improved
Value 1
This fine, efficient processing method enables cost reduction, lead time shortening and the streamlining of supply chains
Ordinary cold forging
SOSEI-FORMA
Value 2
Shear droop is minimized and a smooth, fine surface is produced
Value 3
Yield ratios are improved and resources and energy are saved by omitting cutting processes (CO2 emission is reduced)
Rough forming and tooth/ spline forming
・20% yield improvement
・15% increase in net shaping rate
*Compared with our conventional methods
Seal seating surface, weight reduction, thickening around pins
10% reduction of chain weight
*Compared with our conventional methods
Non-through knurling, inner spline forming, outer ratchet forming
Net shaping rate: 100% (no cutting)
*The technology is applied to parts in various products such as engines, air conditioners and bicycles
We are engaged in technological development through the improvement of die design according to plasticity theories and the optimization of processing conditions, so that press forming can be applied to different shapes and parts that were previously processed via other methods such as cutting.
By combining processing skills produced through our R&D, it has become possible to manufacture products in complex shapes using press forming only. We aim to create added value such as high productivity, cost reduction and energy and material saving.