- リクルートトップ
- プロジェクトD - episode.1
- Chapter.3【生産設計編】
プロジェクトD
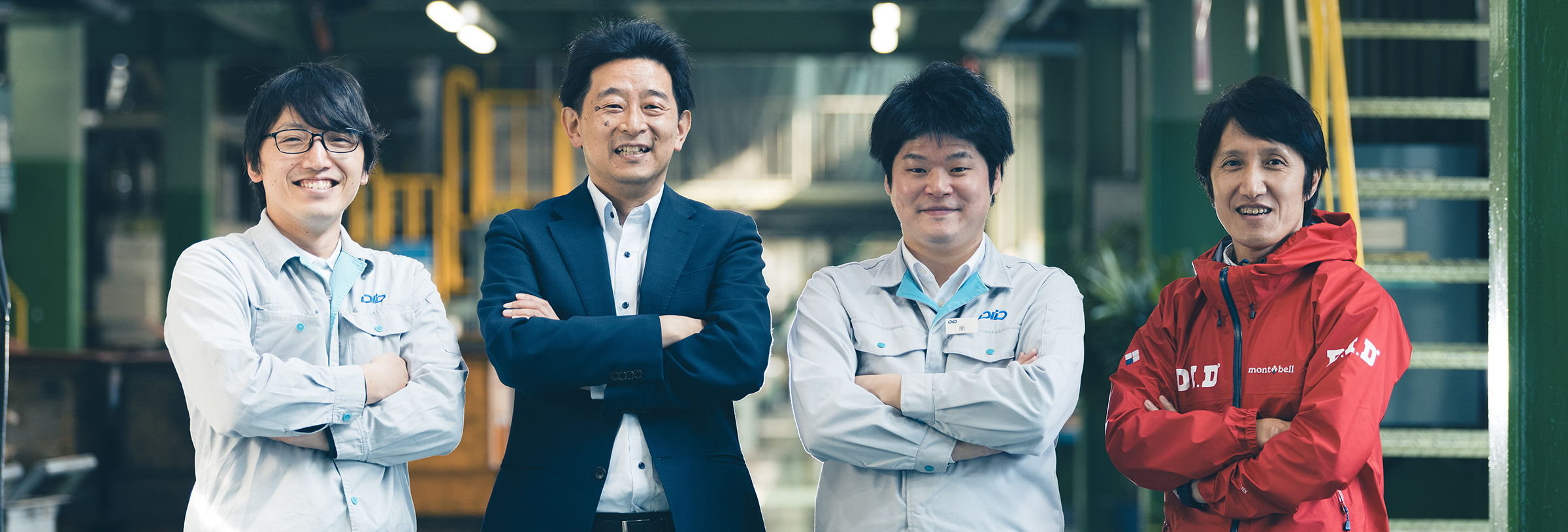
Project D episode.1
MotoGPチェーンプロジェクト
開発×営業×生産技術×商品企画
Chapter.3【生産設計編】
夢の設計を形にしたトライ&エラーの日々
特殊な形状の部品を塑性加工で量産するために、生産技術部門は試行錯誤を続けました。さまざまな課題を乗り越えながら、画期的な製品の実現に一歩ずつ近づいていきました。
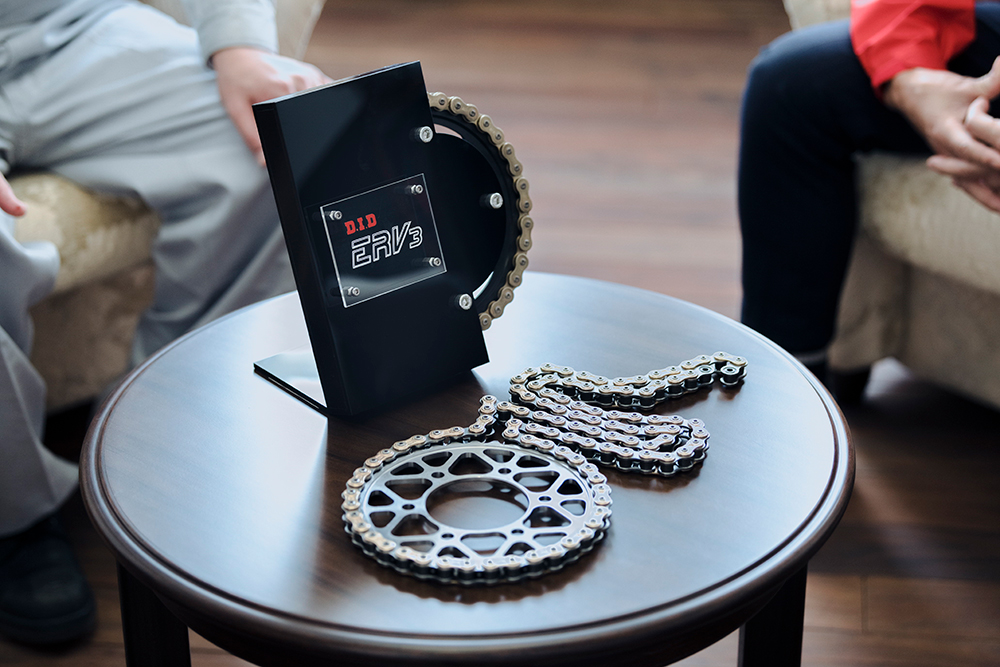
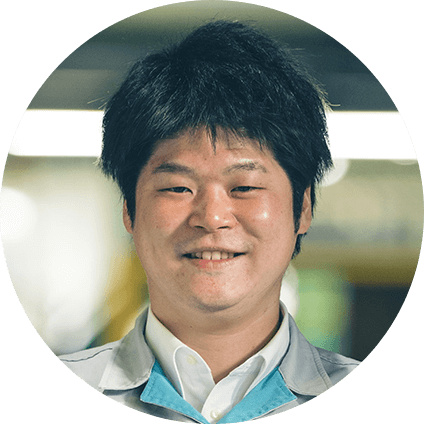
塑性加工で部品をつくるのは、例えるなら粘土細工と同じです。最初の工程で細部まで細かい形状をつくってしまうと、後工程で大きな加工をするときに歪みが出てしまいます。
形状の違う複数のツールで材料の形を整えていく際には、どの順番で加工するのかを慎重に考えなければいけません。金型部品はとても高価で多額の費用がかかることもあり、不用意な失敗だけはしないように、どのような生産工程にするかは頭をしぼりましたね。目標とする開発完了時期が迫る中で、時間との勝負でした。
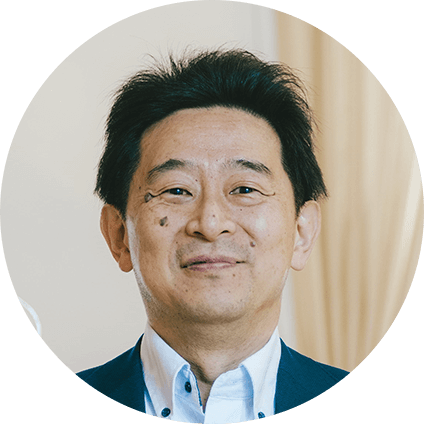
急がせてしまって申し訳なかったね。先方がとても乗り気で「すぐにでも使いたい」とおっしゃっていたこともあって、できるだけ早く塑性加工の試作品をテストに持っていきたかったんだよ。
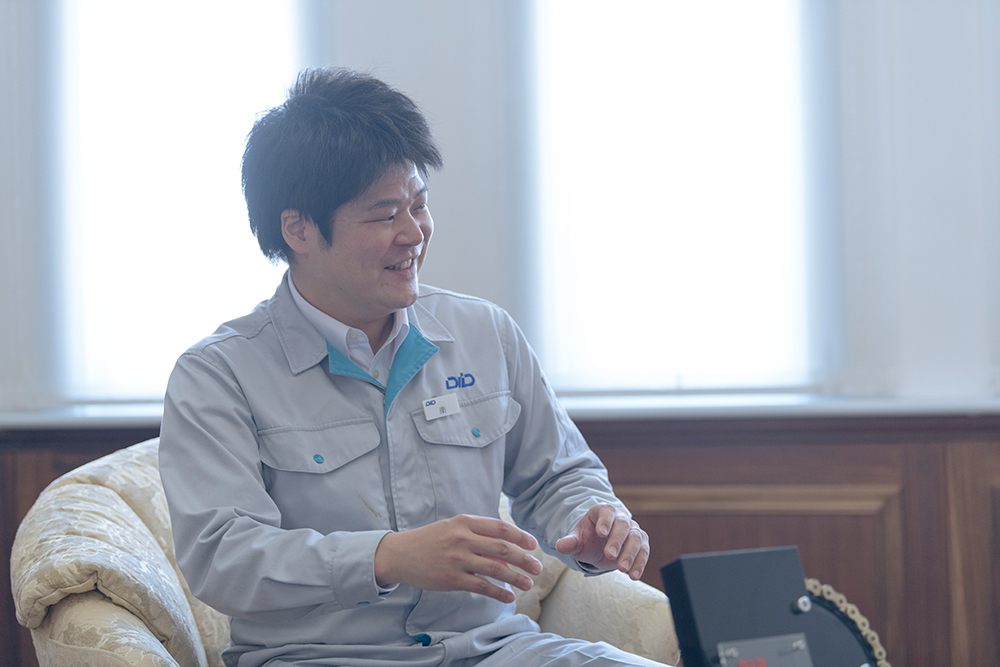
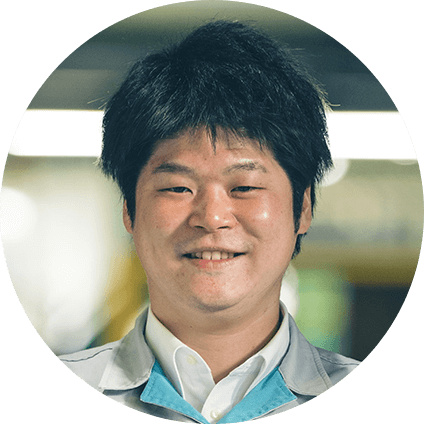
そこはお客様の要望でもあるので、頑張りました。ただ、最大の問題は納期の短さじゃなかったんです。2018年当時は、うちの会社はまだプレス鍛造をしていなかったので、工場には生産に必要なプレス機がありませんでした。
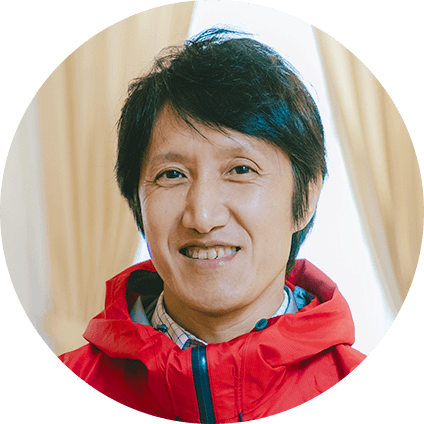
ああ、そうか。今「520ERV6」の加工に使っている福田工場のプレス機は、2020年に新工場棟と一緒に導入した機種だもんね。
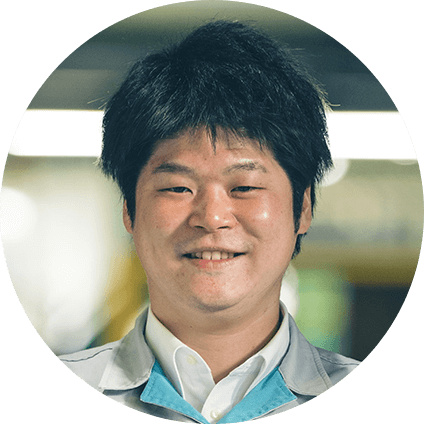
ええ。それが入るまでは、試作用のプレス機をどこかからお借りする必要がありました。幸い、僕が技術研修でお世話になった長野県の会社にある機械を使わせてもらえることになったんですが、長野まで出向いて慣れない環境での作業には、どうしても不自由は感じました。
試作も最初につくった金型では思うように加工できないこともありました。それでもめげずに、2度3度と試作を繰り返して、設計開始から半年かけて、ようやく性能評価が可能な完成度になりました。
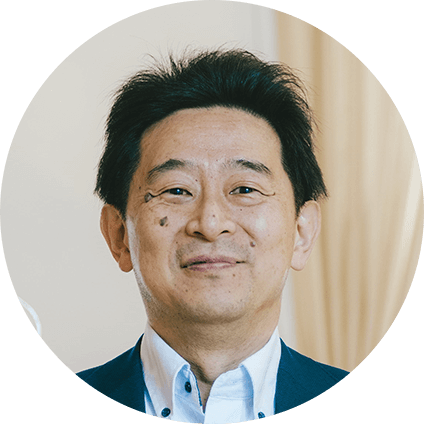
おかげで2019年から、いよいよ試験走行による実走評価を始められたわけだね。
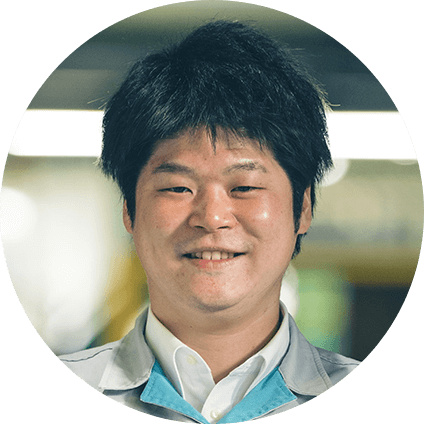
そこからもまた大変でしたよ。試験走行用の試作品は、限られた量の材料で規定数のチェーンを用意しなければならないので、製造を失敗できないプレッシャーがありましたし。試験の回数を重ねて、製造量が増えていくと、金型の疲労や摩耗による成形トラブルも出てきて、手元にあった金型の予備部品も使い切るほど、いつもギリギリの状況で生産をつないでいました。
試作ではそのような環境でしたので、新工場が建った2020年から自社の機械で加工できるようになったときは本当にうれしかったですね。
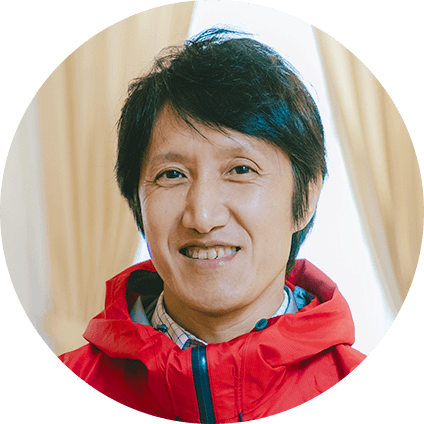
「520ERV6」が2020年シーズンから正式採用されて、MotoGPを走るマシンに使われるようになったのは、開発者のみんなのそういう努力があったからなんだなあ。翌年にはそのチームの選手がシーズンチャンピオンになって、チェーンの実力を証明してくれたしね。
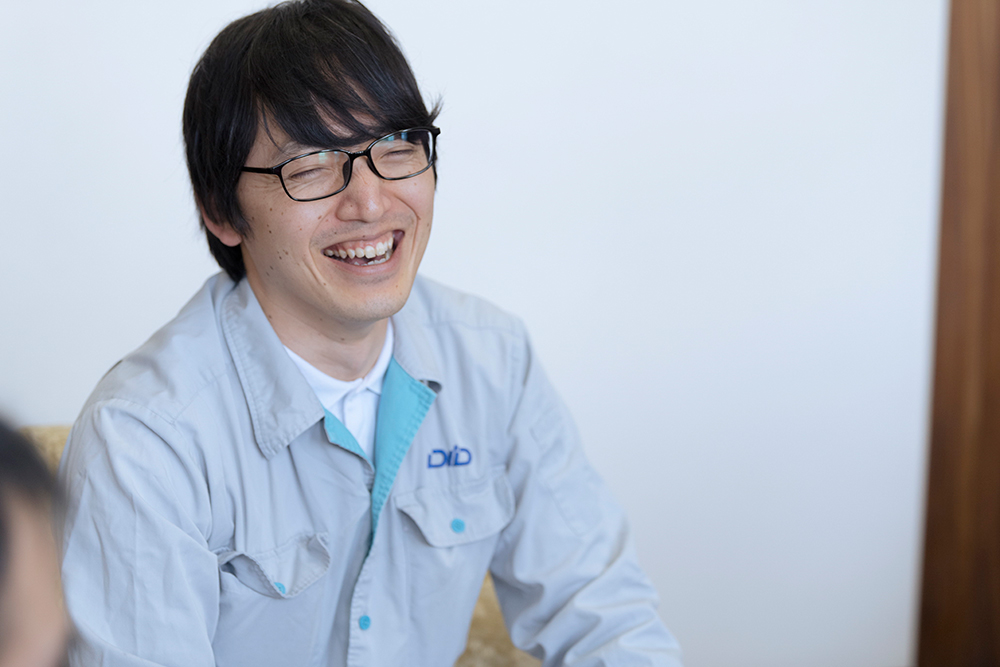
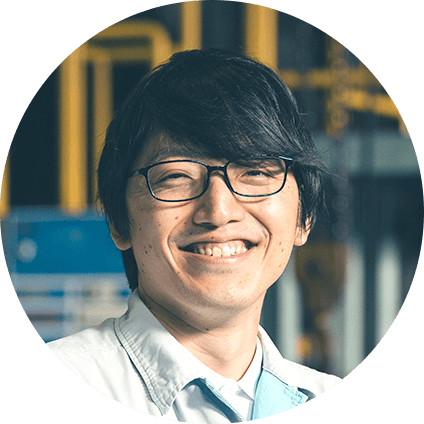
南くんは僕にも何度もチェーンの形状について相談しに来てくれてましたよ。僕ら開発部門が技術の粋を注ぎ込んだこのチェーンが製品の形になったのも、南くんをはじめとする生産技術部門が根気強く量産の実現に取り組んでくれたからだと思います。